Smart cooking interventions for sustainable palm sugar production
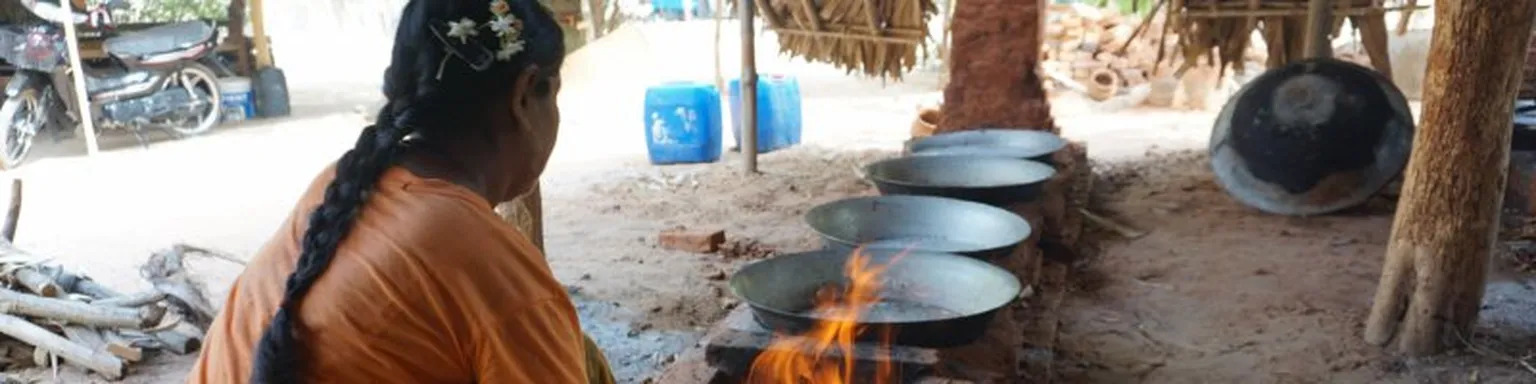
Context
Since the palm sugar supply chain in Myanmar has become linked to Unilever’s global markets, the demand has grown. However, the use of biomass to process the sugar has also increased, creating significant pressure on local ecosystems and contributing to climate change through increasing greenhouse gas emissions.
To tackle this challenge, SNV and Zawgyi Premier – a company active in the global procurement of agricultural products – are taking action to develop the market for fuel-efficient cookstoves. This project is funded by TRANSFORM, a foundation led by DFIT and Unilever. The following blog details the significant results achieved through this intervention improving the livelihoods of the farmer households and reducing environmental pressure.
Harvesting of palm sugar trees.
There is a deep traditional connection within Burmese culture to the cultivation and harvesting of palm sugar trees. Providing a primary income source for many poor households in the central dry zone of Myanmar, it is an activity that requires full family involvement during the 8 to 9 month harvest season from February to September.
Twice a day in low season, the men of the household climb 20-30 trees and as many as 60 trees in the high season (April to July). This requires going up as high as 15 meters to collect the precious sap (nira). The women and young children then cook the nira to remove the liquids by heating and stirring, until it is solid jackery. This process can take them anywhere between 2 and 6 hours a day, depending on the number of trees harvested and the volumes of nira collected.
The palm sugar cookstoves vary in design from 3 to 6 pots, chimney or no chimney, sunken or raised, brick or stone, fuel feed or no fuel feed, all facilitating a standardised production method with varying degrees of efficiency, safety and functionality. Each of these cookstove designs use between 40 to 80 kgs of wood per day for the heating process; this has a significant impact at a household level on budget and time, and at an environmental level resulting in deforestation and raised greenhouse gas emissions.
Production process
At the beginning of the process, the sap is evenly distributed amongst the pots, and the fire is lit. As the heat inside the stove increases and flows through the system, it transfers energy to the pots, evaporating off the excess moisture. With the fire chamber concentrated under the first two pots, these have the fastest evaporation rate and the cooks carefully control the balance between heat and volume until the sugar begins to caramelise after roughly 90 minutes.
At this point, fuel loading is stopped and by using the latent heat from the embers and constantly stirring, burning of the sugar is prevented. Once the nira takes on a viscous texture it is removed from the stove and the stirring continued until the last of the moisture is extracted by air drying, bringing the moisture content down to below 7%. It is then molded.
As each completed pot is removed, the other pots with their pre-warmed nira are moved down and a fresh pot is added to the stove to repeat the process.
A typical mid-season yield of around 80 litres would require three to four such processes, each taking slightly less time than the last. 12 Kg of sugar can be produced in 2 to 3 hours depending on stove design, fuel type and cooking preference.
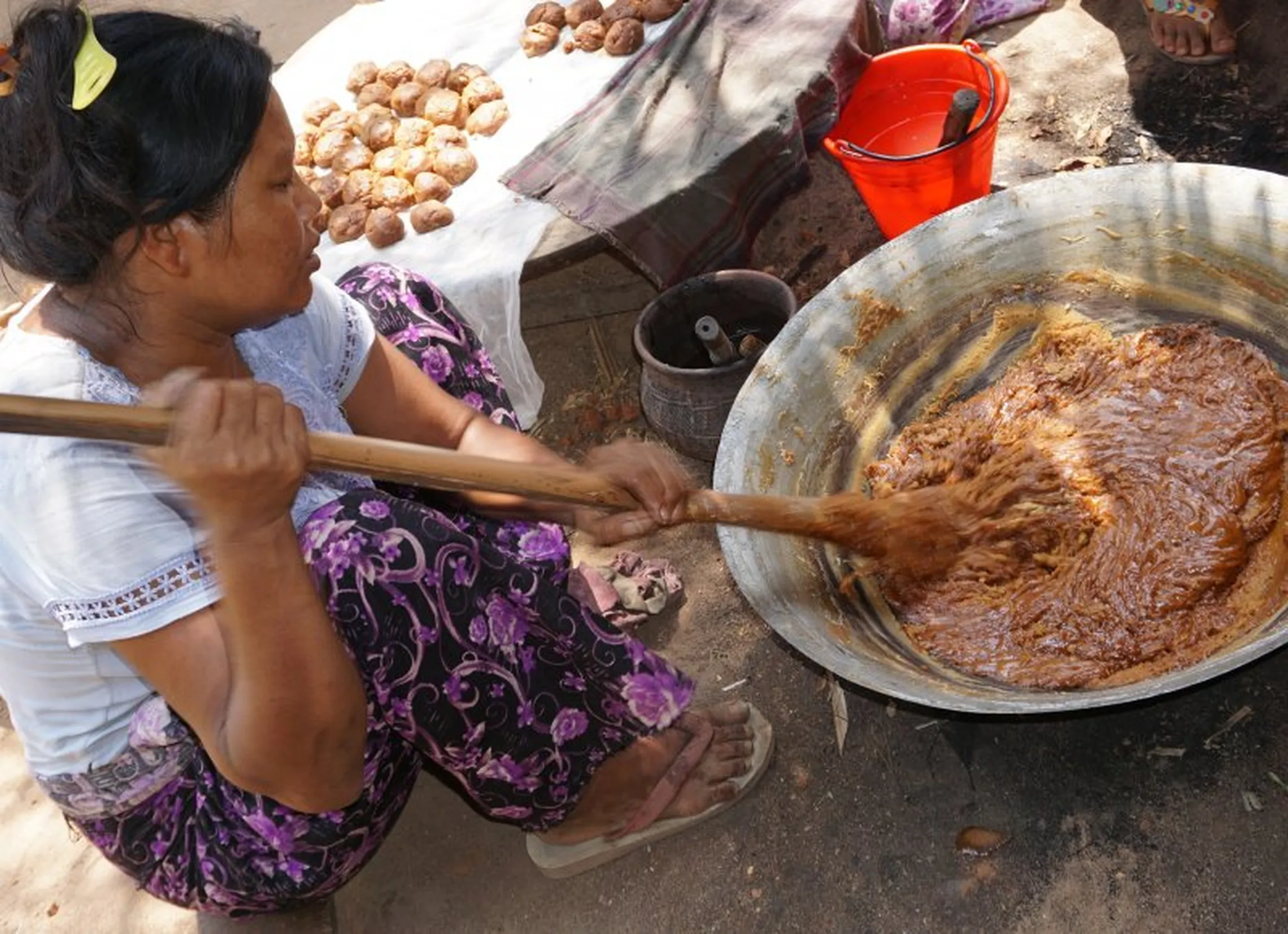
A local farmholder stirs the nira to produce palm sugar in Myanmar (SNV)
The case for Improved Cookstoves.
With a typical smallholding farmer using between 9 and 11.5 tons of wood fuel energy to make 3.6 to 4 tons of palm sugar annually in Myanmar this leaves a significant environmental footprint. Palm sugar production is referred to in local language as the “The Wood Eater”, with its primary energy taken from unsustainable sourced wood, like acacia and palm branches, and secondary sources from agricultural residues. This places excessive strain on the already fragile ecosystems in the Central Dry Zone.
Of the biomass energy consumed, around 40% is foraged and the remaining locally purchased at high prices which can take as much as 25-30% of the households’ gross earnings. For families that are typically just on or below the poverty line of $1.90 US PPP per person, the impact of both the cost of the purchased wood and the time needed to collect foraged wood is significant.
The project study
The feasibility study done by SNV in 2017 gave confidence that the project would achieve a minimum of 20% fuel savings through incremental stove design improvements. The stove model would require minimal behavioural changes and commercial dissemination can be achieved through locally trained artisans.
Building on these insights, the project called Transforming of Production Palm Sugar (ToPPS) will be developed and roll out 300 improved stoves with the purpose of learning and scaling up successful approaches by 2020.
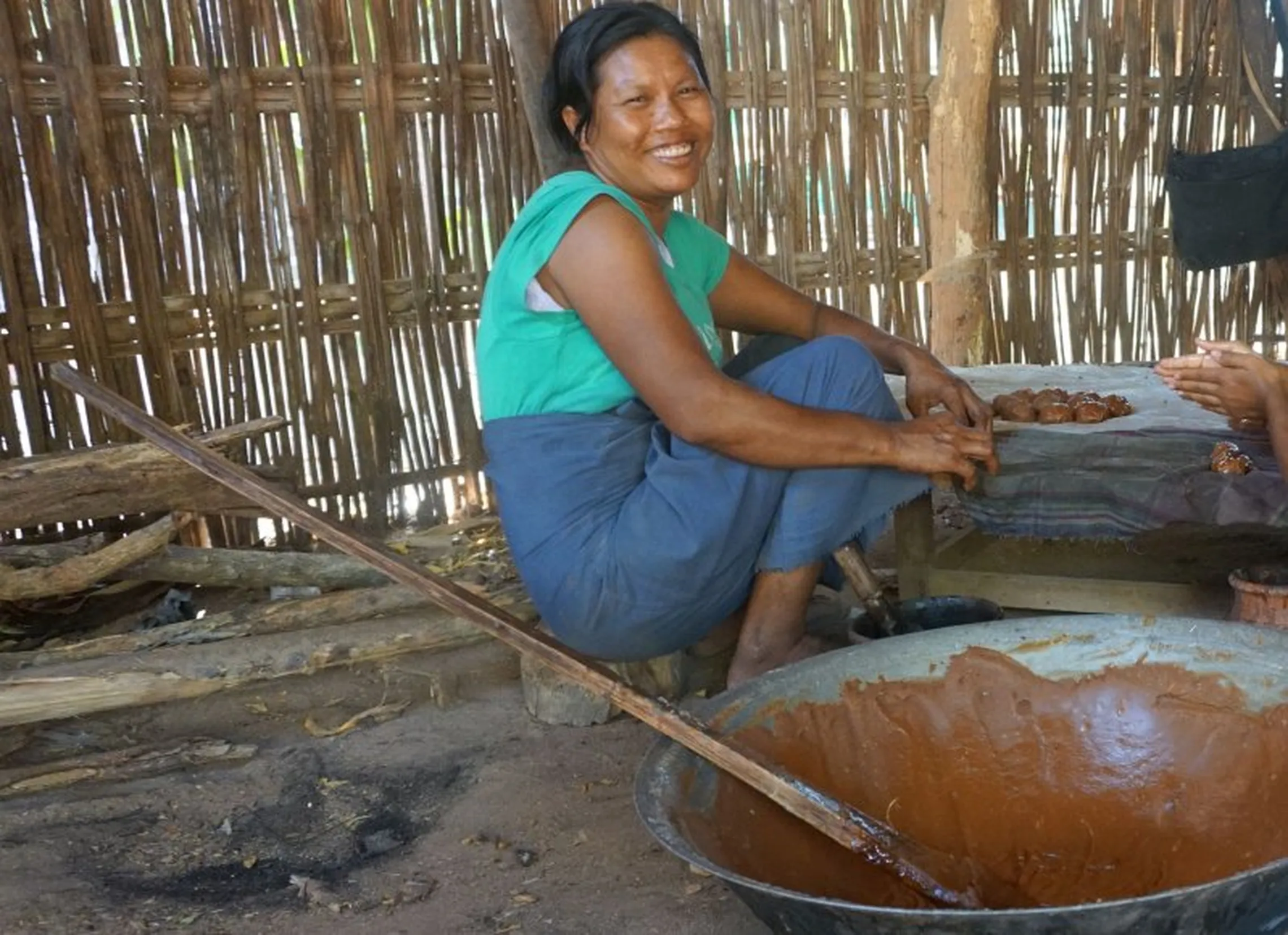
Ms. Aye Aye processing palm sugar into lumps (SNV)
The results
By utilising invaluable local knowledge from palm sugar producers combining with SNV’s global cookstoves experience, a new stove was developed and dubbed the Thet Thar or “Savings Stove”. This stove introduced important designed features that made it superior to currently-used stove models.
First, it contains a smaller fuel entry to prevent over-feeding, which often compromises the stove’s efficiency.
Second, the combustion chamber is shallower to increase the radiation of the char to the pan and encourage greater heat transfer to pots not directly exposed to flames.
And lastly, the pans are sunk deeper into the stove improving the heat transfer.
The Thet Thar stove also provides a duel-grates system to enhance air mixture for better combustion and a chimney designed to control the airflow (thus regulating the heat transferred in the process).
To validate the performance and fuel savings of the new stove model, several tests were performed following the principles of the Controlled Cooking Test as per the protocol from the Alliance for Clean Cooking. The Nga Tha Yauk (baseline stove) and the Thet Thar (new stove) were operated simultaneously to process the same amount of nira with the same amount of fuel.
After a typical processing activity for 12 kilogrammes of sugar, the testing results indicated savings of more than 10 Kg of wood against 42 Kg, reducing 25% of fuel consumption in comparison. It is worth pointing out that the Nga Tha Yauk baseline was identified as the best available alternative, and the savings will be greater for other models that are popular in the region.
Furthermore, the cooking process took 18 minutes less or 12% time savings with the new improved stove (from 149 minutes to 131 minutes), and the wood saved translates to 6 tons of CO2 equivalent on greenhouse gas emissions per stove per year. This is as much as two persons flying from Myanmar to the UK and back again.
The new cookstove model requires 12 hours to assemble and an investment of 66 USD for materials and labour costs; this is 20 USD more expensive than the Nga Tha Yauk model with a minimum shelf life of 3 years with annual low cost/free maintenance.
However, this investment is worthwhile for the farming family with a payback period of just 3 months on savings. This project, therefore, presents a very significant positive change in the palm sugar industry regarding socio-economic development and environmental protection.
What is next?
The next steps for the project team will be to replicate the lessons of the first 45 stoves and to monitoring usage in high and low season. This will allow us to finalise the design and bring the best available product to market for the tens of thousands of families making a living from the Myanmar palm sugar industry.
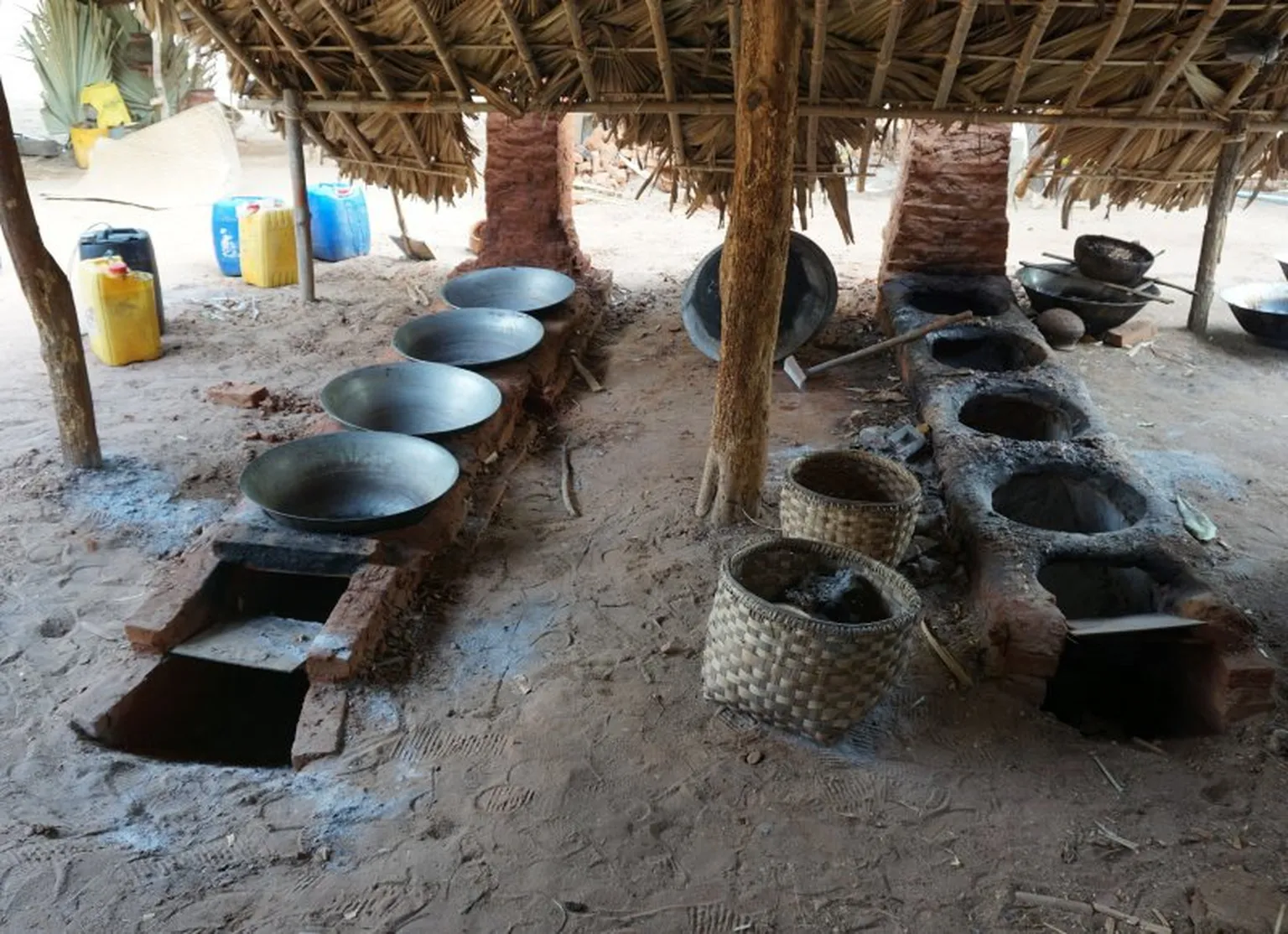
The cooking test. The Thet That model left, the Nga Tha Yauk model right. (SNV)
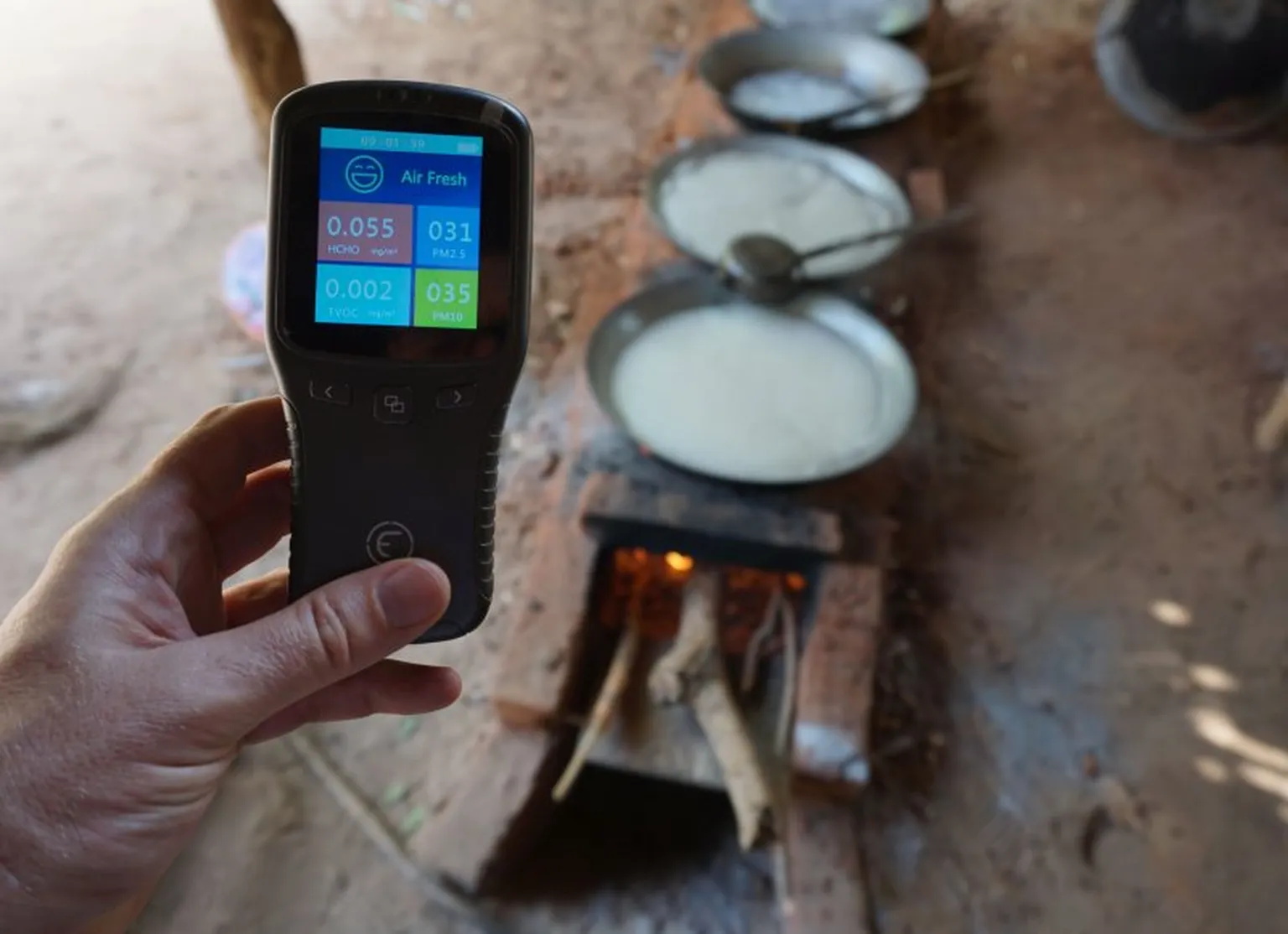
Testing the process (SNV)
The promising results from these tests have progressed the project to the next phase, where the Thet Thar stove will be disseminated among 60 smallholders; then it will reach up to 300 farmers through trained artisans. It will be linked to a micro-credit scheme that lowers the initial investment barrier.
The 100,000 palm sugar producers in Myanmar offer a significant opportunity to replicate and scale up the market of fuel-efficient cookstoves among smallholders supplying palm sugar to Zawgyi and other supply chains. In addition to finding ways to improve the livelihoods of poor smallholders and to lower environmental footprints.